Low-CI Ethanol Made From Milk

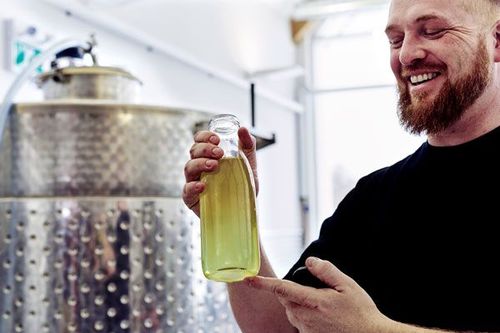
Lakhimpur Khiri: A farmer’s seminar in Kodari village was hosted by the sugar mill, cane department, and Cane Research Institute. Participants, including officials and scientists, provided technical information on disease prevention, advanced sugarcane varieties, and pest control. Farmers learned about the trench method for planting and schemes offered by the cane department. Dr. Praveen Kumar Kapil and Dr. RD Tiwari emphasized using balanced fertilizers and avoiding prohibited varieties for effective crop maintenance.
Corn starch is far and away the most common ethanol feedstock in the United States—94%, according to the U.S. Department of Energy—however, throughout the years, a variety of other feedstocks, ranging from corn stover to wheat straw to milo, have been used. One distillery is utilizing an unusual feedstock, one experimented with during the 1970s oil crisis, to make ethanol.
Milk permeate is a byproduct made when milk is filtered for a variety of products. The process begins with removing fats for butter and ice cream production, leaving behind skim milk. To make it efficient for cheese and yogurt manufacturers, some dairies concentrate the remaining skim milk even further, retaining the proteins and separating out the milk permeate, a mixture of water and lactose. Although it is typically disposed of through animal feed, the sugar content in lactose makes it a great feedstock for alcohol production, explains Omid McDonald, founder of Dairy Distillery. He originally founded the company to use milk permeate as a feedstock for vodka, making a product branded Vodkow.
“The way we got into this was my cousin had come back from his local dairy farm, and they were talking about excess milk being dumped, and I said, ‘Whoa, can that be turned into alcohol?’ And the idea was to do a craft distillery to make vodka, but very early on I learned just how much of this byproduct is out there, and how it’s a problem for the dairy industry as a whole,” McDonald explains.
McDonald turned to David Geros, a process engineer with experience in cellulosic ethanol production, to explore the economic business model of turning milk permeate into ethanol. In 2021, the Michigan Milk Producers Association, the tenth largest dairy farmer-owned cooperative in the United States, reached out to McDonald about utilizing milk permeate to make vodka. In this case, the feedstock would be a variety of permeate produced via ultra-filtration (UF) at the co-op’s Constantine, Michigan, plant. After realizing that the amount of milk permeate made at the plant would create 47 million bottles of vodka—a volume that would be difficult to sell into the market—Dairy Distillery and MMPA pivoted to ethanol production. Planned to come online in Q1 of 2025, the Constantine facility will make 2.3 MMgy of low-carbon ethanol.
Profitability and Sustainability
Currently, the facility sells the milk permeate to local pig farmers at a very low value—essentially giving it away—explains Joe Diglio, president and CEO of MMPA. “Because we represent dairy farmers, and we take their milk to the marketplace, it was important for us to find an alternative solution,” he says. With consumers’ increased interest in the proteins found in milk, UF systems are becoming more common, and more left-over milk permeate is being made as a result. McDonald explains that it is not necessarily an ideal ingredient for pig farmers: a limited amount of it can be fed to the pig, and it is a challenge for farmers to handle the byproduct in its liquid form. “This is not a huge amount of ethanol like the corn guys [produce],” McDonald says. “We’re not going after corn ethanol; this is a way for dairy to be able to get into a new market and diversify their portfolio. As Joe [says], it’s about finding value, but also resiliency. It allows them to have a revenue stream that’s totally independent from the dairy side, which just provides more resiliency and safety for their members.”
Turning the milk permeate into low-carbon ethanol is a great opportunity for MMPA to advance its decarbonization efforts. As the project was being designed, Dairy Distillery commissioned EcoEngineers to do the carbon accounting for the project; an important step for determining the carbon intensity of the fuel and the profitability of the project. Completing this step has been time consuming due to the amount of paperwork involved, Diglio explains.
MMPA started pursuing this project before the Inflation Reduction Act became a reality, but it was “lucky” timing for the project developers. Half of the project’s cost is attributed to the biogas production process that is eligible for IRA investment tax credit support, McDonald says. The ethanol’s low CI number of 15 gives it opportunities in several markets, from the SAF industry to the low-carbon fuel programs in California, Canada and other areas. “A lot of the folks that [will] utilize the product coming off of Constantine’s … production [are] looking to attach themselves to a project like this to get the creditability established with the sustainable message that we’re creating,” Diglio says.
Process Design
Lactose fermentation is an unusual process, but it has been done before, McDonald explains. In the ’70s and ’80s, dairy producing countries like Ireland and New Zealand experimented with the process to make ethanol to help ease the supply pressure caused by oil shortages. However, many of those facilities shut down because they were unable to compete with corn-based ethanol production. Dairy Distillery started working with the University of Ottawa to research lactose fermentation in 2017 and has spent the last five years developing the process.
McDonald outlines the steps involved in moving milk permeate from the milk producer to the distillery, and the processing needed to turn it into ethanol. First, the milk permeate will be piped from the dairy under the road over to the distillery. Then, it will be pumped into fermentation tanks, and yeast will be added to ferment the lactose into ethanol. After that, the ethanol is sent to the stills to be concentrated and separated, and finally, purified for use as an on-road fuel or SAF feedstock. The waste stream will be sent to an anerobic digester that turns it into biogas used to power the stills. After it is run through the aerobic digester, the water is then treated and discharged into the river.
There are several advantages of using milk permeate as a feedstock; for example, it already contains all the water needed for fermentation and there is no milling step required, explains McDonald. This means feedstock processing requires only a small amount of energy, keeping the carbon intensity of the final product low. However, the biggest benefit is the fact that the byproduct is a waste stream, so the ethanol production does not need to account for any upstream carbon impact coming from producing the milk permeate. “Another advantage is after we finish our fermentation [and] distillation process, our waste stream is put into a digester that generates biogas to power all the energy needed for the stills to further reduce the carbon intensity,” McDonald says. “So … it’s actually a carbon-neutral sugar, and a very efficient production process that gets our CI so low.” According to calculations, the ethanol produced at the Constantine plant will be 15 grams of CO2 per megajoule, most of that number comes from Michigan’s electrical grid, which is not as clean as some other states.
The disadvantage of using a waste feedstock is that the volume of feedstock available is typically finite. However, the Constantine facility is a great fit for the technology because, due to its ultrafiltration system, the plant produces a good amount of accessible, continuously available byproduct.
Although the volume of ethanol produced is limited, the decarbonization potential made this project an important step toward achieving MMPA’s sustainability goals. Every ton of permeate that gets converted to ethanol displaces a ton of carbon, McDonald says. “Constantine produces about 16,000 tons of permeate that will create a displacement of [in the end] 16,000 tons of carbon, which represents about 10% of the carbon footprint of the milk that’s produced at Constantine,” he continues. “So, that’s sizeable, maybe one of the largest dairy decarbonization projects out there, and MMPA has a lot to be proud of leading that charge.”
Community Impact
As part of this project, MMPA will leave the Constantine municipality’s wastewater system, instead combining the ethanol plant and dairy facility’s wastewater to produce natural gas, cleaning the remaining water and pumping it back to the river afterward. “We built one single system that takes our distillation waste and the waste from the dairy, produces biogas, which powers the stills, and then cleans the water to river quality,” McDonald says. “And it just discharges to the local river. So, truly it [works like this]: permeate comes in with waste from the dairy and out comes low-carbon ethanol and water to discharge to the river.
The plant has several community impacts, including new local jobs, decreased traffic and decarbonization. It will create 12 full-time jobs and remove the truck traffic that was needed to send the milk permeate to local farmers. “You’re having basically two plants side by side, which gives this plant the opportunity to continue to expand, continue to innovate, and I think that adds an element to the community as a good steward of a business operation that can generate opportunities for those that live around the area,” Diglio says.
The project has received support from the local government because of the benefits it brings to the community, being granted $2 million by the Michigan Business Development Program along with a 15-year State Essential Services Assessment exemption worth $682,500, according to a press release from the Michigan Economic Development Corporation.
Demand for milk and other dairy products free of lactose has increased in recent years, Diglio says. Although it remains to be seen whether that trend is here to stay, UF systems’ are a valuable efficiency improvement, helping dairy processors produce cheese and other products that don’t need the water in the milk. As these systems are being implemented in the U.S. and Canada, Dairy Distillery’s lactose fermentation process is an opportunity for dairy farmers to find new value from this waste stream. Moving forward, McDonald hopes to expand Dairy Distillery to dairies across the U.S. and Canada, helping dairy producers maximize value.
“There’s an opportunity for this technology, which has been pioneered through the leadership of MMPA, to be bolted onto dairies across the U.S. [and] here in Canada,” McDonald says. “MMPA’s leadership has gotten the attention of Canadian dairies who often look to the U.S. for guidance, and so to provide both value and decarbonization, which are both central to what all dairy processors need to do.”
Source Link : https://ethanolproducer.com/articles/low-ci-ethanol-made-from-milk
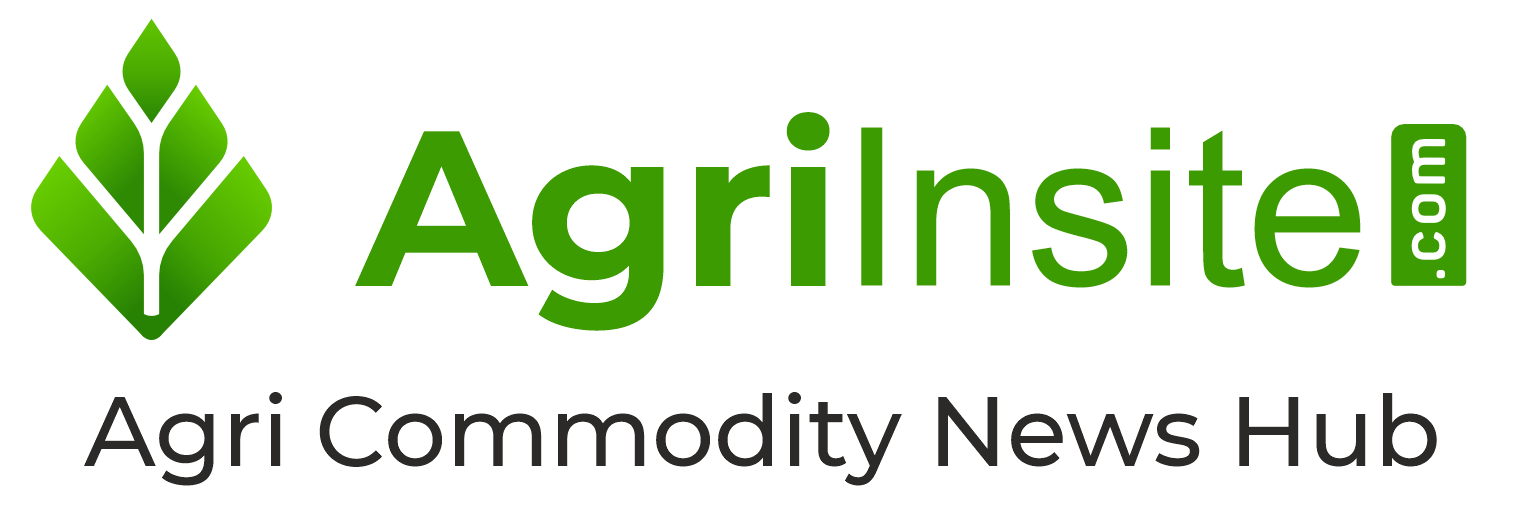