Ethanol-Based Blendstock Ready to Flow

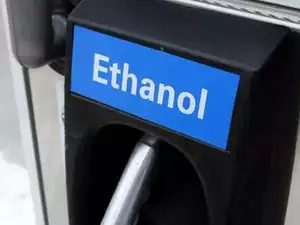
Oak Ridge National Laboratory’s CADO technology, developed to overcome the ethanol blend wall, transforms ethanol into a versatile blendstock for gasoline, diesel, or jet fuel using a unique zeolite catalyst. The U.S. EPA approved this renewable gasoline blendstock in May 2024. Vertimass LLC, which licensed the technology, plans to commercialize it by integrating it into existing ethanol plants. This advancement facilitates higher ethanol usage in fuels and opens new market routes for cellulosic ethanol.
From the beginning, the CADO technology developed by scientists at Oak Ridge National Laboratory was meant to be an ethanol blend-wall breaker. CADO stands for conventional alcohol deoxygenation and oligomerization—a process that ORNL first studied in its Tennessee labs about 15 years ago.
“I got challenged by management,” says Brian Davison, ORNL’s chief scientist for systems biology and biotechnology. “They asked what we could do to deal with the ethanol blend wall (i.e., to get past 10% ethanol in the U.S. gasoline pool).”
Davison and other scientists working with him explored the idea of converting ethanol into other things. On their list of must-have characteristics, the team agreed that a product that was water stable and didn’t require the use of hydrogen during production would be ideal. It was the work of a catalytic chemist that set their early effort in the right direction and helped them discover a novel catalyst capable of producing a drop-in blendstock suitable for gasoline, diesel or jet fuel. The blendstock, they determined, could be made from any form of pure alcohol, including the most ubiquitous, commercial type—corn ethanol.
“In 2010, we knew it was going to work,” Davison says. Now, a decade-and-a-half later—a timeframe Davison says is respectable for bringing new biotechnology to market—the ORNL team has another reason to celebrate their work. It all started as a simple idea initially meant to give ethanol producers a way to break through the perceived production limit created by the E10 maximum volume policy of the time. Today, the idea is on the precipice of becoming a market-ready technology that companies and ethanol producers alike may soon be able to tap into.
In May, the U.S. Environmental Protection Agency approved the registration of a renewable gasoline blendstock that is produced through a process based on that original work at ORNL by Davison and others. It’s welcome news to Vertimass LLC, a company that has licensed the ORNL CADO technology process and catalyst, positioning the platform at the center of its growth plan.
Making An Ethanol-Based Blendstock
At the heart of the ORNL and Vertimass technology is a unique catalyst made from low-cost metals and zeolite. The mineral zeolite contains aluminum and silicon compounds that are used for many things ranging from dry agents to air purifiers. In some instances, zeolite products are used for personal health purposes like balancing pH to remove heavy metals in the body.
The zeolite catalyst chosen by the original ORNL team was porous and absorbent. From an ethanol feedstock, the catalyst is able to produce a longer hydrocarbon chain. Because the zeolite catalyst can produce lengthier hydrocarbon chains, the need for some of the traditional production steps were eliminated. “Contrary to long-held assumptions,” the ORNL team says, “an energy-consuming, separate intermediary dehydration step converting ethanol to ethylene was not required for the conversion.”
From the very beginning of their work, Davison and his team were achieving a near-total conversion of the ethanol feedstock into hydrocarbons, he says. “But it wasn’t always the hydrocarbons you wanted.”
In the early days, the blendstock created via ethanol would create a significant amount of ethylene. Although the byproduct was valuable, the researchers knew it wouldn’t be an easy product for ethanol producers to manage.
Over time, the research team was able to dial in their catalyst choice to feature what they call a “hydrocarbon pooling effect.” According to Davison, inside the catalysts are pores that create this pooling once the liquid enters. “We think the pore size and the mouth size of the catalysts play a role in that [pooling] process,” he says.
Because the pooling effect is so important to the process, the ORNL researchers performed labeling experiments using a hydrogen isotope to track the molecular transition. In simple terms, they were able to test and confirm that the hydrocarbon pooling mechanism was in fact working and crucial to the process.
Once the catalysts permeate another porous support surface that provides stability and keeps the catalysts from washing out with the liquid products, substantive production can be achieved. “This is a one-time, one-place reaction,” Davison says, explaining that the environment created by the process “lowers the energetics” of the transactions to the right level, making a one-step reaction possible. In an overly simplified explanation of the process, he says, ethanol goes in and renewable blendstock comes out. The product looks similar to gasoline. When tweaked, it can also be made to look like diesel or JP-8 (military fuel).
The renewable blendstock production approach is able to operate at lower temperatures. While reaction temperatures for ethanol are generally in the 350 degree Celsius and above range, the CADO process only requires a range that can start at 250 degrees Celsius. In addition, the process does not require hydrogen. And dehydration is not required to upgrade the ethanol into the blendstock.
“One of the things we found early on was that by having a water-stable catalyst, we could eliminate the molecular sieve,” Davison says. “We could run a 90% ethanol, 10% water solution through.”
In a scientific paper the team published early on, they noted that fermentation streams at any stage of purification can be converted into blendstock. Impurities in the ethanol stream, they said, did not impact the performance of the catalyst, meaning partially concentrated ethanol streams can be used for upgrading to blendstock—and expensive dewatering is not necessary.
Ready for the Market?
One of the many challenges faced by Davison and his team was getting buy in, not necessarily from their ORNL colleagues and others working directly on the project, but from outside researchers and ethanol experts. Internally, the research was continuously supported financially by the Center for Bioenergy Innovation at ORNL and the DOE Office of Science. The DOE Office of Energy Efficiency and Renewable Energy was also a big supporter. Outside institutions and research labs eventually played a part in further testing and verification of the process before and after Vertimass licensed the process in 2014.
The real issue for the team was getting others to believe in the one-step process. “People didn’t believe it [was valid and realistic] because it [wasn’t performed] using a traditional multi-step process,” he says, explaining that the technology simply didn’t fit traditional thinking in the late 2000s.
“It challenges a long-held but incorrect assumption,” says ORNL scientist Chaitanya Narula. “It has been assumed that you must go from ethanol to ethylene, which is endothermic and requires energy. We showed [that] this step doesn’t occur, and that the overall reaction is slightly exothermic.”
Eventually, Davison and his team say the liquid fuels research community—including those with funding ability—began to realize that if the cellulosic ethanol movement was going to work, there had to be a way to get more ethanol into the market. The blend wall had to be broken through, one way or another, he says.
The EPA’s decision to approve the renewable gasoline blendstock this year means that the process is proven and everything is, as Davison puts it, ready to go. “The EPA announcement hits the mark that there is a market for this,” he says.
To get the renewable gasoline blendstock into the market, Davison and the team at Vertimass believe ethanol plants currently in production can add bolt-on technology to diversify their ethanol into two streams. One stream of ethanol will go into the traditional gasoline blending market and the other will become a feedstock for renewable gasoline.
Vertimass is ready to fully commercialize the technology. Several entities from around the world have shown interest, including UGI Corp., which entered into an agreement with Vertimass to produce SAF from an ethanol feedstock for sustainable aviation fuel (SAF). The goal of the joint venture is to build 20 plants over 15 years.
“Starting with technology developed at a national lab—with the foundation of that scientific expertise—gave us an excellent starting point for refining and commercializing the technology,” says John Hannon, COO of Vertimass. “Having that initial technology verification and intellectual property has been essential.”
Since obtaining the intellectual property for the process a decade ago, Davison says Vertimass has substantially improved the selectivity and stability of the catalysts. Blue Biofuels Inc., another advanced biofuels production company looking to become an early adopter of the process, formed a partnership with Vertimass early this year. Their new company, VertiBlue Fuels LLC, is owned equally by both. The goal for VertiBlue is to build an SAF plant in Florida using sugarcane as a feedstock to produce ethanol.
Vertimass also has plans to take its CADO approach outside the U.S. Last year the company purchased Ekobenz, a Poland-based company that was one of the first biorefineries in Europe. The Ekobenz facility provides Vertimass with a commercial-scale site to deploy its CADO tech to produce SAF for the European market.
Davison, who is a patent holder for the original process and a cofounder of Vertimass, is excited about the recent EPA approval. He’s also pleased with the attention Vertimass and the CADO process are now receiving, a sort of validation of his longtime work.
It has taken a lot to get the original idea from that challenge about breaking the blend wall back in 2009 to a real bolt-on possibility at operational ethanol plants. It’s been a long road to success made possible by many collaborators: scientists, post-docs, students, legal professionals and more. And even though the first eight years of the work was performed at ORNL, several other entities have played a hand.
“As a scientist, I’m happy to see the excitement around this, and also for others to see the arc it takes to get a process like this moving forward,” he says. “It takes an original idea and people that don’t take no for an answer.”
Without getting into specific numbers on the cost of installation and potential ROI, Davison says the economics of adding a CADO-based bolt-on technology to an existing ethanol plant look favorable. CADO-derived blendstocks could potentially be blended at 20 percent with petroleum-based jet fuel, he explains, based on the aromatics limits currently in place. For gasoline it could be more. The process now offered by Vertimass has made it possible for the use of more ethanol in the general fuel mix. It’s also given cellulosic ethanol another route to market once it is developed at scale. And either way, the research and commercialization efforts, including everything that may result from it, Davison says, just shows there is always another way for ethanol and science to breakthrough.
Source Link : https://ethanolproducer.com/articles/ethanol-based-blendstock-ready-to-flow
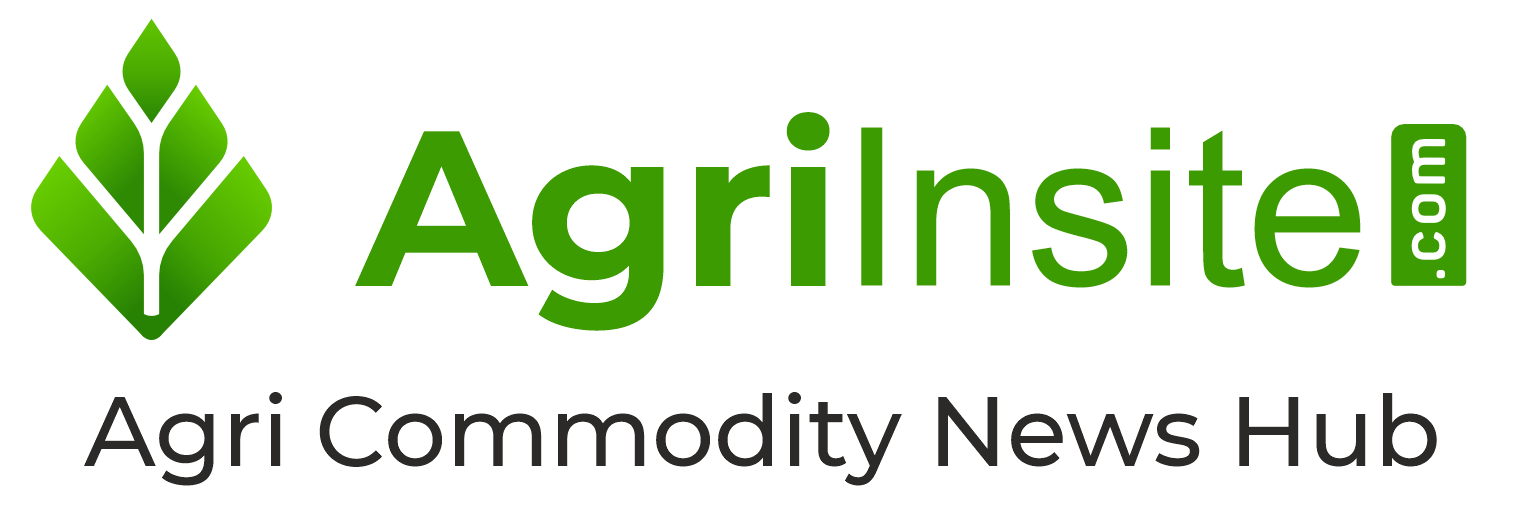