Cost analysis of sugar factories from the management point of view

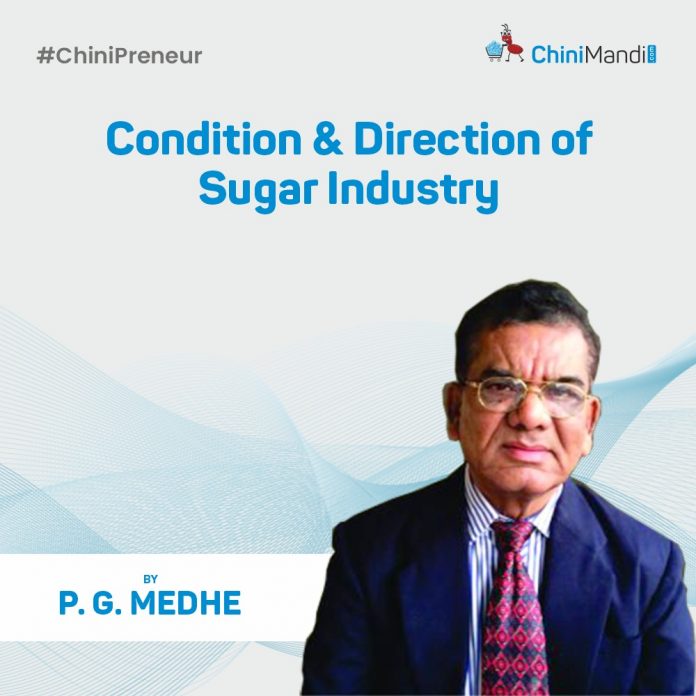
In the dynamic landscape of the sugar industry, effective cost management is pivotal for sustaining profitability and competitiveness. This article delves into the intricate process of cost analysis within sugar factories, emphasizing the managerial perspective. By examining the various cost components, from raw material procurement to production and distribution, we aim to uncover strategies that can optimize operational efficiency and financial performance
In the dynamic landscape of the sugar industry, effective cost management is pivotal for sustaining profitability and competitiveness. This article delves into the intricate process of cost analysis within sugar factories, emphasizing the managerial perspective. By examining the various cost components, from raw material procurement to production and distribution, we aim to uncover strategies that can optimize operational efficiency and financial performance. Through a detailed exploration of fixed and variable costs, economies of scale, and cost control mechanisms, this analysis provides valuable insights for managers seeking to enhance their decision-making processes and drive their factories towards greater economic success.
COMPONENTS OF COST –
AGRICULTURAL INPUT COSTS: Agricultural input costs are a significant component of the overall cost structure in the sugar industry, often representing up to 80% of the total production cost. Here are the key elements that contribute to these costs:
Seed and Planting Costs –
Sugarcane: As a perennial crop, sugarcane requires substantial initial investment in high-quality seed stock and planting operations. Mechanical planting is common, and preparations include selecting the best possible seed-stock and applying fertilizers and minerals.
Fertilizers and Soil Amendments: Fertilizer costs are a major expense, particularly nitrogen-based fertilizers, which are essential for crop development. The cost of fertilizers is closely linked to natural gas prices, impacting the overall cost structure.
Irrigation: Sugarcane crops benefit significantly from irrigation, which can enhance yields. Precision irrigation techniques, including drip irrigation, fertigation, are employed to optimize water and nutrient delivery.
Pest and Disease Management: Effective pest and disease management is crucial, especially in the early stages of crop development. Integrated pest management strategies and the application of protective measures are necessary to maintain healthy crops.
Harvesting Costs: Harvesting sugarcane and sugar beet involves significant labor and machinery costs. The timing and method of harvesting can impact the overall efficiency and cost.
Fuel and Energy Costs:The cost of fuel for machinery and transportation is another critical factor. Rising fuel prices can significantly increase the cost of agricultural operations.
Understanding and managing these input costs is essential for sugar factory managers to maintain profitability and competitiveness in the market. By optimizing these elements, they can achieve better yields and reduce overall production costs.
PROCEEDING COST : Processing costs in sugar factories encompass a variety of expenses associated with converting raw sugarcane into white Crystal sugar. Here are the key components…
Labor Costs: Wages and benefits for factory workers, including those involved in operations, maintenance, and quality control, form a significant part of processing costs.
Energy Costs: Sugar processing is energy-intensive, requiring substantial electricity and fuel for machinery, boilers, and other equipment. Energy costs can fluctuate based on fuel prices and energy efficiency measures.
Maintenance and Repairs: Regular maintenance and repairs of machinery and equipment are essential to prevent breakdowns and ensure smooth operations. This includes costs for spare parts and technical services.
Chemicals and Additives: Various chemicals and additives are used in the processing stages, such as lime, sulfur dioxide, and flocculants, which help in clarifying and purifying the sugar.
Water Usage: Large quantities of water are used in the washing, extraction, and purification processes. Costs associated with water supply, treatment, and disposal are significant.
Packaging and Storage: Once processed, sugar needs to be packaged and stored. This includes costs for packaging materials, storage facilities, and handling equipment.
Depreciation: The depreciation of factory buildings, machinery, and equipment is accounted for as a part of processing costs. This reflects the wear and tear over time and the need for eventual replacement.
Quality Control: Ensuring the quality of the final product involves costs related to laboratory testing, monitoring, and compliance with industry standards.
Logistics and Distribution: Costs associated with transporting the finished product to markets, including fuel, vehicle maintenance, and logistics management.
By effectively managing these processing costs, sugar factory managers can enhance operational efficiency and profitability. Regular reviews and optimization of these cost components are crucial for maintaining a competitive edge in the industry.
OPERATIONAL COSTS: Operational costs in sugar factories, particularly those related to ongoing expenses like utilities and administrative costs, are crucial for maintaining smooth and efficient operations. Here are the key components:
Utilities –
Electricity: Sugar processing is energy-intensive, requiring substantial electricity for machinery, lighting, and other equipment. Efficient energy management can help reduce these costs.
Water: Large quantities of water are used in washing, extraction, and purification processes. Costs include water supply, treatment, and disposal.
Fuel: Boilers and other equipment often rely on fuel, which can be a significant expense. Fuel costs can fluctuate based on market prices.
Administrative Costs-
Salaries and Wages: This includes the compensation for administrative staff, including managers, accountants, and clerical workers2.
Office Supplies and Equipment: Regular expenses for office supplies, computers, and other equipment necessary for administrative functions2.
Insurance: Costs for various types of insurance, including property, liability, and health insurance for employees.
Legal and Professional Fees: Expenses for legal services, auditing, and other professional services required for compliance and operational efficiency.
Communication: Costs associated with telecommunication services, internet, and other communication tools.
Maintenance and Repairs: Regular maintenance of office buildings and administrative equipment to ensure they remain functional and efficient2.
Miscellaneous Administrative Expenses –
Travel and Transportation: Costs for business travel, including transportation, accommodation, and meals.
Marketing and Advertising: Expenses related to promoting the factory’s products and maintaining its market presence.
Effectively managing these operational costs is essential for maintaining profitability and ensuring the smooth functioning of the sugar factory. Regular monitoring and optimization of these expenses can lead to significant cost savings and improved operational efficiency.
COST EFFECTIVENESS IN ADMINISTRATIVE EXPENSES: Managing administrative costs effectively is crucial for sugar factories to maintain profitability and operational efficiency. Here are some strategies commonly employed:
Automation and Technology: Implementing automated systems for tasks such as payroll, inventory management, and accounting can reduce the need for manual labor and minimize errors.
Utilizing enterprise resource planning (ERP) software helps integrate various administrative functions, improving data accuracy and decision-making.
Streamlining Processes: Simplifying and standardizing administrative procedures can reduce redundancy and improve efficiency. This includes optimizing workflows and eliminating unnecessary steps.
Regularly reviewing and updating administrative processes to ensure they remain efficient and relevant.
Outsourcing Non-Core Activities: Outsourcing tasks such as IT support, human resources, and legal services can be more cost-effective than maintaining in-house teams.
Partnering with specialized firms allows access to expert services without the overhead costs associated with full-time staff.
Energy Efficiency: Implementing energy-saving measures in office buildings, such as LED lighting, energy-efficient HVAC systems, and smart thermostats, can significantly reduce utility costs.
Encouraging energy conservation practices among staff can also contribute to lower energy consumption.
Negotiating Supplier Contracts: Negotiating long-term contracts with suppliers for office supplies, utilities, and other services can help stabilize costs and secure better rates.
Regularly reviewing supplier contracts to ensure competitive pricing and service quality.
Training and Development: Investing in training programs for administrative staff can improve their efficiency and productivity, leading to cost savings.
Cross-training employees to handle multiple roles can provide flexibility and reduce the need for additional hires.
Regular Financial Reviews: Conducting regular financial audits and reviews helps identify areas where costs can be reduced or optimised.
Using financial data to make informed decisions about budget allocations and cost-cutting measures.
By implementing these strategies, sugar factories can effectively manage their administrative costs, ensuring that resources are used efficiently and contributing to overall profitability.
COST MANAGEMENT TECHNIQUES: Effective cost management in sugar factories can be significantly enhanced through preventive maintenance and energy efficiency measures. Here’s how these techniques can be applied:
Preventive Maintenance –
Scheduled Inspections and Servicing: Regularly scheduled inspections and servicing of machinery and equipment help identify potential issues before they lead to costly breakdowns. This proactive approach ensures that all equipment operates efficiently and reduces downtime.
Condition Monitoring: Implementing condition monitoring technologies, such as vibration analysis and thermal imaging, allows for real-time tracking of equipment health2. This helps in predicting failures and planning maintenance activities accordingly.
Standard Operating Procedures (SOPs): Developing and adhering to SOPs for maintenance tasks ensures consistency and thoroughness. This includes detailed checklists for routine inspections and maintenance activities.
Training and Skill Development: Regular training programs for maintenance staff ensure they are equipped with the latest knowledge and skills to perform preventive maintenance effectively. This reduces the likelihood of human error and enhances overall maintenance quality.
Energy Efficiency –
Energy Audits: Conducting regular energy audits helps identify areas where energy consumption can be reduced. This includes assessing the efficiency of boilers, motors, and other energy-intensive equipment.
Optimising Equipment Operation: Ensuring that equipment operates only when necessary and at optimal settings can significantly reduce energy consumption. This includes using variable frequency drives (VFDs) to control motor speeds and implementing automated control systems.
Upgrading to Energy-Efficient Equipment: Investing in energy-efficient machinery and equipment, such as high-efficiency boilers and motors, can lead to substantial energy savings over time3. Although the initial investment may be higher, the long-term savings justify the cost.
Insulation and Heat Recovery: Proper insulation of steam lines, boilers, and other heat-generating equipment minimizes heat loss3. Additionally, implementing heat recovery systems can capture and reuse waste heat, further improving energy efficiency.
Lighting and HVAC Systems: Upgrading to LED lighting and energy-efficient HVAC systems can reduce electricity consumption3. Implementing smart controls for lighting and climate control ensures these systems operate efficiently.
By integrating these preventive maintenance and energy efficiency strategies, sugar factories can effectively manage operational costs, enhance equipment reliability, and reduce energy consumption. This not only improves profitability but also contributes to sustainability efforts.
IMPLEMENTATION OF EFFECTIVE CONDITION MONITORING: Implementing condition monitoring effectively in sugar factories involves several key steps and technologies to ensure machinery operates efficiently and to prevent unexpected breakdowns. Here’s how sugar factories can achieve this:
- Adopting Advanced Sensors and Monitoring Systems –
Vibration Sensors: These sensors detect abnormal vibrations in machinery, which can indicate potential issues such as misalignment or bearing failures.
Temperature Sensors: Monitoring the temperature of critical components helps in identifying overheating issues that could lead to equipment failure.
Pressure Sensors: These are used to monitor the pressure in boilers and other equipment, ensuring they operate within safe limits.
- Utilizing Condition Monitoring Software –
Integrated Platforms: Software like System 1® from Bently Nevada integrates data from various sensors, providing a comprehensive view of equipment health.
Real-Time Data Analysis: These platforms offer real-time data analysis and diagnostics, enabling quick decision-making and proactive maintenance.
- Implementing Predictive Maintenance –
Data Analytics: Using historical data and predictive analytics to forecast potential failures and schedule maintenance activities before issues arise.
Machine Learning: Advanced algorithms can learn from data patterns to predict equipment failures more accurately.
- Regular Training and Skill Development –
Staff Training: Regular training programs for maintenance staff on the latest condition monitoring technologies and best practices ensure they are well-equipped to handle the systems.
Workshops and Certifications: Encouraging staff to attend workshops and obtain certifications in condition monitoring and predictive maintenance.
- Remote Monitoring and Diagnostics-
Wireless Sensors: Implementing wireless sensors allows for remote monitoring of equipment, reducing the need for manual inspections.
Cloud-Based Solutions: Using cloud-based platforms for data storage and analysis enables remote access to condition monitoring data, facilitating quick responses to potential issues.
- Regular Audits and Reviews-
Performance Audits: Conducting regular audits of the condition monitoring system to ensure it is functioning correctly and providing accurate data.
Continuous Improvement: Using audit results to make continuous improvements to the monitoring system and maintenance practices.
By integrating these strategies, sugar factories can effectively implement condition monitoring, leading to improved equipment reliability, reduced downtime, and lower maintenance costs.
EFFECTIVE FINANCIAL MANAGEMENT: Effective financial management in sugar factories involves meticulous budgeting, forecasting, and cost comparison to ensure profitability and sustainability. Here’s an overview of these key aspects:
Budgeting and Forecasting –
Operational Budget: This includes detailed projections of all operational expenses such as raw material costs, labor, utilities, maintenance, and administrative expenses. It helps in setting financial targets and allocating resources efficiently.
Capital Budget: This focuses on long-term investments in infrastructure, machinery, and technology upgrades. It ensures that the factory is well-equipped to meet future production demands and maintain competitiveness.
Cash Flow Budget: This tracks the inflow and outflow of cash to ensure liquidity and the ability to meet short-term obligations. It helps in managing working capital effectively.
Sales Forecasting: Predicting future sales based on historical data, market trends, and economic indicators2. Accurate sales forecasts help in planning production schedules and inventory management.
Expense Forecasting: Estimating future expenses by analyzing past spending patterns and considering factors like inflation and changes in raw material prices. This helps in identifying potential cost-saving opportunities.
Scenario Analysis: Creating different financial scenarios (best case, worst case, and most likely case) to prepare for various market conditions. This aids in strategic planning and risk management.
Cost Comparison –
Benchmarking: Comparing the factory’s costs with industry standards and competitors to identify areas of improvement. This includes analyzing costs related to raw materials, processing, labor, and logistics.
Regular benchmarking helps in understanding the factory’s competitive position and implementing best practices to reduce costs.
Cost Analysis –
Variable Costs: These are costs that vary with production levels, such as raw materials and energy consumption. Monitoring and controlling variable costs can lead to significant savings.
Fixed Costs: These are costs that remain constant regardless of production levels, such as salaries, rent, and insurance. Efficient management of fixed costs ensures better financial stability.
Cost per Unit: Calculating the cost per unit of production helps in pricing strategies and profitability analysis. It involves dividing total costs by the number of units produced.
Global Cost Comparison: Analysing the cost of production in different regions to understand global competitiveness. For instance, Brazil has lower production costs compared to Europe and China due to factors like lower labor costs and higher yields.
Understanding regional cost differences helps in strategic decisions regarding exports and market expansion.
By integrating these budgeting, forecasting, and cost comparison techniques, sugar factories can enhance their financial management practices, leading to improved profitability and sustainability.
IMPACT IF COST COMPARISON IN DECISION MAKING: Cost comparison plays a crucial role in decision-making within sugar factories, influencing various aspects of operations and strategic planning. Here’s how it impacts decision-making.
- Identifying Cost-Saving Opportunities –
Benchmarking: By comparing costs with industry standards and competitors, sugar factories can identify areas where they are overspending. This helps in pinpointing specific processes or inputs that can be optimized for cost savings.
Efficiency Improvements: Cost comparison highlights inefficiencies in production processes, prompting managers to implement changes that reduce waste and improve productivity.
- Strategic Planning –
Investment Decisions: Understanding cost structures allows managers to make informed decisions about where to invest in new technologies or equipment. For example, if energy costs are high, investing in energy-efficient machinery can be justified.
Resource Allocation: Cost comparison helps in prioritizing resource allocation to areas that offer the highest return on investment. This ensures that capital is used effectively to enhance overall profitability.
- Pricing Strategies –
Competitive Pricing: By comparing production costs with those of competitors, sugar factories can set competitive prices for their products. This is crucial for maintaining market share and profitability.
Cost-Plus Pricing: Understanding the detailed cost structure allows for accurate cost-plus pricing, ensuring that all costs are covered while achieving desired profit margins3.
- Risk Management-
Cost Volatility: Regular cost comparison helps in identifying volatile cost components, such as raw materials or energy. This enables managers to develop strategies to mitigate these risks, such as securing long-term supply contracts.
Scenario Planning: Comparing costs under different scenarios (e.g., changes in raw material prices or energy costs) helps in preparing for potential market fluctuations and economic conditions.
- Operational Efficiency –
Process Optimisation: Detailed cost comparison can reveal inefficiencies in production processes, leading to targeted improvements. For instance, if labor costs are high, automation might be considered to enhance efficiency.
Maintenance and Upkeep: Comparing maintenance costs with industry benchmarks can highlight areas where preventive maintenance could reduce long-term expenses.
- Sustainability Initiatives –
Environmental Impact: Cost comparison can also include the analysis of environmental costs, such as waste management and energy consumption. This encourages the adoption of sustainable practices that can reduce costs and improve the factory’s environmental footprint.
Regulatory Compliance: Ensuring that cost structures align with regulatory requirements helps in avoiding fines and penalties, which can be costly.
By leveraging cost comparison, sugar factories can make more informed and strategic decisions, ultimately leading to improved efficiency, profitability, and sustainability.
INFLUENCE OF MARKET DYNAMICS ON PRICING STRATEGIES: Market dynamics significantly influence pricing strategies in various ways. Here’s how these dynamics impact pricing decisions.
- Supply and Demand Fluctuations –
Supply: When supply exceeds demand, prices tend to fall as businesses compete to sell their excess inventory. Conversely, when demand exceeds supply, prices rise due to scarcity.
Demand: Changes in consumer preferences, seasonal trends, and economic conditions can affect demand. For example, higher demand during festive seasons can lead to price increases.
- Competitor Actions –
Competitive Pricing: In highly competitive markets, businesses often engage in price wars to attract customers. This can lead to lower profit margins but higher sales volumes2.
Differentiation: In markets where products are differentiated, companies can use premium pricing strategies based on perceived value and unique features.
- Consumer Behavior –
Price Sensitivity: Understanding how sensitive customers are to price changes helps businesses set optimal prices. For instance, if customers are highly price-sensitive, even small price increases can lead to significant drops in sales.
Perceived Value: Pricing strategies can be influenced by how much value consumers perceive in a product. Higher perceived value can justify higher prices.
- Technological Advancements –
Dynamic Pricing: Technologies like AI and machine learning enable dynamic pricing, where prices are adjusted in real-time based on market conditions, competitor prices, and consumer behaviour. This helps businesses maximize revenue and stay competitive.
Cost Reduction: Technological improvements can reduce production costs, allowing businesses to lower prices while maintaining profitability.
- Regulatory Changes –
Taxes and Subsidies: Government policies, such as taxes on raw materials or subsidies for certain products, can affect pricing strategies. For example, subsidies can lower production costs, enabling lower prices.
Price Controls: For the sugar Industry government imposes price controls to protect consumers, which limits setting of prices.
- Economic Trends –
Inflation: Rising inflation can lead to higher production costs, which businesses may pass on to consumers through higher prices.
Recession: During economic downturns, businesses might lower prices to stimulate demand and maintain sales volumes.
By understanding and adapting to these market dynamics, businesses can develop effective pricing strategies that enhance competitiveness and profitability.
CASE STUDY OF THE SUGAR FACTORY WHO HAVE IMPLEMENTED COST SAVING MEASURES:
SHRE CHHA. SHAHU SSK LTD, KAGAL, KOLHAPUR –The Shree Chhatrapati Shahu Sahakari Sakhar Karkhana, commonly known as Shahu Sugar Factory, is a prominent cooperative sugar mill located in Kagal, Kolhapur. Established in 1980, the factory has played a significant role in the economic development of the region, particularly benefiting the local farmers and community.
Key Achievements and Initiatives –
High Recovery Rates: Shahu Sugar Factory is known for its high sugar recovery rates, which have consistently placed it among the top cooperative sugar mills in Maharashtra. This efficiency is a result of adopting advanced agricultural practices and high-yield cane varieties.
Energy Efficiency: The factory has implemented several energy-saving measures, including the use of bagasse (a by-product of sugarcane) for power generation. This not only reduces energy costs but also promotes sustainable practices.
Water Management: Advanced water recycling systems have been installed to minimize water usage and reduce costs associated with water procurement and treatment. This initiative has also helped in maintaining environmental sustainability.
Marketing and Export: Shahu Sugar Factory has a dedicated marketing department that focuses on developing institutional buyers in the domestic market and exporting a significant portion of its production. The factory has been recognized as a “STAR EXPORT HOUSE” by the Commerce Ministry of India for its remarkable achievements in sugar export3.
Community Development: Beyond its industrial activities, the factory has contributed significantly to social causes. It supports local sports, education, and cultural activities, reflecting its commitment to the overall development of the community.
Awards and Recognition –
Best Cooperative Sugar Factory Award: The National Federation of Cooperative Sugar Factories has awarded Shahu Sugar Factory for its high recovery rates and overall efficiency.
Efficiency Awards: The factory has received multiple awards for its maximum export of sugar, highlighting its excellence in production and export activities,
Shahu Sugar Factory’s success is a testament to the effective implementation of cost-saving measures and sustainable practices. Its contributions to the local economy and community development make it a model for other cooperative sugar mills in the region.
GUIDING INSTITUTE FOR COST REDUCTION: The Vasantdada Sugar Institute has been instrumental in guiding several cooperative sugar factories in Maharashtra towards cost reduction.
Optimising Cane Procurement: By improving the logistics of cane transport and reducing the time between harvesting and processing, scientific Harvesting & Transport program, factories have minimized losses and improved efficiency.
Energy Efficiency: Implementing energy-saving technologies in boilers and turbines has significantly reduced fuel consumption.
Modernisation of Machinery: Upgrading to modern, automated machinery has reduced labor costs and increased production efficiency.
Computerisation: Proving the ERP software suitable for the sugar factories resulting in reduction in wage bill.
In conclusion, the cost analysis of sugar factories from a management perspective reveals a multifaceted approach to achieving operational efficiency and financial sustainability. By implementing innovative cost-saving measures such as optimizing cane procurement, enhancing energy efficiency, modernizing machinery, and leveraging by-products, sugar factories can significantly reduce expenses and improve profitability. The case study of the sugar factory and guiding Institute in Maharashtra, including the exemplary practices of Shahu Sugar Factory, underscore the importance of strategic planning and continuous improvement. These efforts not only bolster the economic viability of the factories but also contribute to the broader goals of sustainability and community development. As the industry evolves, the adoption of such best practices will be crucial in navigating the challenges and seizing the opportunities that lie ahead.
P.G. Medhe is the former Managing Director of Shri Chhatrapati Rajaram Sahakari Sakhar Karkhana Ltd and sugar industry analyst. He can be contacted at +91 9822329898.
To read more about Sugar Industry continue reading Agriinsite.com
Source : Chinimandi
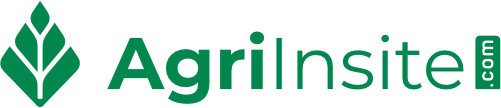