Built For Mars, Used For Ethanol

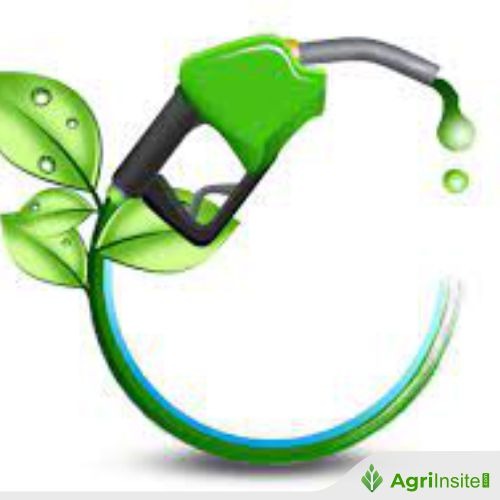
Originally built to measure Mars’ atmosphere, Keit’s rugged IRmadillo spectrometer is now transforming ethanol production. Designed to withstand rocket launches, it delivers real-time, vibration-resistant mid-infrared analysis of fermentation, sugars, acids, and ethanol levels. With installations across North America, IRmadillo helps producers boost yields, cut fermentation times, and detect issues early—proving space-ready tech can thrive in the toughest earthly industries.
Keit Industrial Analytics’ in-line process liquid analyzer technology now used in many U.S. ethanol plants was originally intended to take measurements of the Martian atmosphere.
The small group of optical physicists and engineers who started Keit wanted to create a system to measure the mid-infrared spectrum using a notoriously fragile process. They knew the analysis would work in space, but they also knew the traditional systems wouldn’t survive a launch.
“The main reason stuff gets up to space and doesn’t survive is because of the launch,” says Dan Wood, CEO of Keit.
After creating a stable, sensitive instrument capable of surviving the physical abuse of a launch, Wood and his team realized they’d made a robust piece of electronics that could take measurements in harsh environments. Today, the U.K.-based company serves several industries that had all but discarded the idea of using mid-infrared spectrometry to measure liquids, including oil and gas, pulp and paper, chemical manufacturing, industrial biotechnology, food and drink, pharmaceuticals and ethanol production. The technology is aptly named the IRmadillo, a reference to its size and ability to go almost anywhere.
From Mars to Wisconsin
Keit is a spin-off company of the European Space Agency Business Incubation Centre UK. After the company’s tech survived a satellite take-off, Keit went to work developing a system that could capture sensitive measurements.
Early venture capital investors in Keit were so impressed with the capabilities of the technology that they invested without knowing which industries the company would eventually serve. Although Wood has worked with clients in several industries, ethanol was seen as an early fit. Today, the company serves ethanol producers in Europe and North America.
Keit started by performing testing for a start-up firm looking at producing propanediol. With positive results in hand, the company partnered with a large enzyme supplier that wanted Keit’s tool because of its ability to validate product performance for ethanol clients.
“You can see biochemistry happening in real-time,” Wood says of its tech.
Unlike traditional high performance liquid chromatography (HPLC) products, IRmadillo provides more than just snapshots of a liquid reaction. For ethanol producers, the tech can show different types of sugars and the levels of organic acids, as well as ethanol and glycerol concentrations in the fermentation tank, all in real-time.
The system is based on a major tweak to the traditional analytical technique known as Fourier transform infrared (FTIR), commonly used to measure how light and chemicals react together in a liquid. The classic FTIR design has been around for more than a century and relies on a pair of mirrors, one always moving. The light refracts off the mirror system to display various signatures that are then used to reveal the activity in a liquid. According to Keit, the issue with the traditional light measurement approach is that single moving mirror. The necessity of the mirror’s movement means the system is always sensitive to vibrations that can throw it out of balance and reference. Such a system is best suited for an extremely stable bench or lab environment.
The optical physicists at Keit were able to reimagine the setup and get the needed light signatures without the single moving mirror (or lasers and liquid nitrogen cooling sometimes required to obtain such information from light in liquid used with FTIR spectrometry).
The optics inside IRmadillo are free to vibrate because they all move together, and the vibrations of the different components effectively cancel each other out, according to the company. The redesigned approach makes measuring and monitoring continuous processes much easier and more reliable than measuring with conventional instruments, which might need background reference scans every few hours to ensure process balance isn’t disrupted.
Eliminating the fragility from FTIR has allowed industrial clients like ethanol producers to gain a new understanding of liquid reactions not fully possible with interval-based monitoring provided by HPLC systems or the less sensitive NIR (near infrared) systems commonly relied upon.
FTIR is very different from NIR, Wood says, as it is looking at the fundamental molecular vibrations, rather than the second-order effects of those vibrations. Near infrared analysis is like trying to recognize someone by looking at their shadow versus looking at their face. FTIR, unlike NIR, can differentiate the DP3, DP2 and glucose molecules in a mixture.
FTIR not only provides detail, but also speed. Many plants test their fermentation tanks for bacterial infections, yeast issues and other scenarios every eight to 10 hours, Wood says. But problems arise when infections appear at hour 12.
“It could be six hours before you know of an issue,” he says.
In some instances, adding high volumes of antibiotics is the only answer, but it’s possible the yield numbers have already been negatively impacted. Not only can a bad fermentation impact yields, it can also disrupt the settings on the distillation column downstream. So, [it is typically not]just about resolving one issue alone, Wood says.
He says many modern ethanol plants are producing yields in a tight range anyway, but for those looking to increase from 13.8% to 14%, for example, real-time measuring is key.
“For those plants, it’s the small improvements across the facility that matter, rather than avoiding failing fermentations,” Wood says. “You can’t improve what you can’t measure.”
Using a real-time monitoring system isn’t only about saving batches from going bad or becoming less productive. Keit’s system is also able to help producers understand the accurate run times needed for fermentation batches. In one case, a producer using IRmadillo learned that their fermentation times were actually maxed out four hours earlier than they thought. Instead of running fermentation for 48 hours, the producer was able to cut the times to 44 hours, a savings that helped overall throughput, Wood says.
United Wisconsin Grain Producers installed IRmadillo on a recirculation line of a fermenter to track sugars, glycerol, lactic and acetic acids and ethanol. Wood says the technology has illustrated the importance of making changes early, finding solutions to issues before they start.
Installation at Ethanol Plants
Keit designed the small IRmadillo for seamless integration at any ethanol plant, which means the units can be installed directly through existing flanges into tanks, with or without a ball valve for isolation, or fitted into recirculation pipework. All of the units communicate directly with a plant’s DCS.
The units can be used in any of six common areas: monitoring and optimizing enzymatic breakdown in the slurry tank; monitoring enzymatic breakdown in the liquefaction tanks; watching or controlling propagation in the propagation tank; monitoring or controlling fermentation; monitoring distillation columns; and monitoring and optimizing final drying steps between the molecular sieve and ethanol storage tanks.
Keit is carrying out a trial to monitor propagation and fermentation at the same time, Woods says.
“One of the areas many plants do not understand fully is when to send prop out to fermentation,” he says. “Most producers just say they do it at a certain time. Most will acknowledge they don’t really know.”
Keit will sell directly to clients or perform test trials for producers that want to see for themselves how the units will work within their existing system. Units can also be rented. Most units are roughly $100,000, including set-up and initial training. Keit has already hired a 20-year ethanol industry veteran out of Iowa to install IRmadillos and help with any questions.
Customer-validated models have shown that the units pay for themselves in under a year, according to Keit. Saving one fermentation batch from a lactic acid infection could cover the costs. A benefits calculator from Keit often shows producers can save more than $1 million per year.
But Woods is most proud of the results from industry surveys he sends to clients after installation.
“We survey them to find out how we did. We consistently get an 8.8 out of 10. We get a lot of comments that say we give a lot of good support. You can’t afford to be bad people to work with.”
Keit is already working with producers to develop new dashboards for monitoring all the units at a plant to help assess and optimize the production process.
Every unit is outfitted with a diamond tip probe for safety and accuracy in clean-in-place procedures.
Other Options
Although Keit is working to help producers understand their next-level tech and why it exceeds the limitations of HPLC, Wood still advocates for producers to continue running their HPLC set-ups. Proven and high-performance HPLC suppliers currently working in the ethanol space include Metrohm, PerkinElmer and Chrom Tech Inc.
Metrohm provides NIR spectrometry systems along with HPLC systems. NIR technology is often used with non-contact measurements of solids (like protein levels in grain before grinding into flour) or water measurements in aprotic solvents.
PerkinsElmer provides many ethanol labs with HPLC and benchtop analysis equipment well-suited for sample testing. Most systems require minimal training and maintenance. The company’s NIR analyzers are typically installed to measure continuous product optimization or moisture after grain drying.
Chrom Tech now provides an advanced HPLC system that reduces the standard analysis run time of 20 minutes by up to one-third. The company also has an HPLC column design that allows the testing column to last longer.
Keit works with ethanol plants to provide their IRmadillos as pre-calibrated analyzer units or as a tool based on a plant’s common HPLC results.
The company has come a long way from its work developing methodology to test the atmosphere and conditions on Mars, Wood says. The ethanol industry has become an earthbound fit for its space-capable technology because of IRmadillo’s standout ability to take detailed and accurate measurements.
It seems the industry’s push to find efficiencies and collect more data landed at the perfect time for Keit’s tech, Wood says. “We’ve essentially designed a highly capable spectrometer system that will go where no spectrometer has gone before.”
To read more about Ethanol Industry & Bio Energy News, continue reading Agriinsite.com
Source : Ethanol Producer Magazine
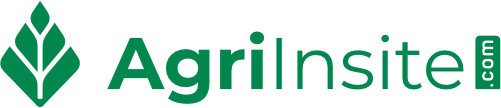