Inside Staverton: The Times and the Shredded Wheat factory

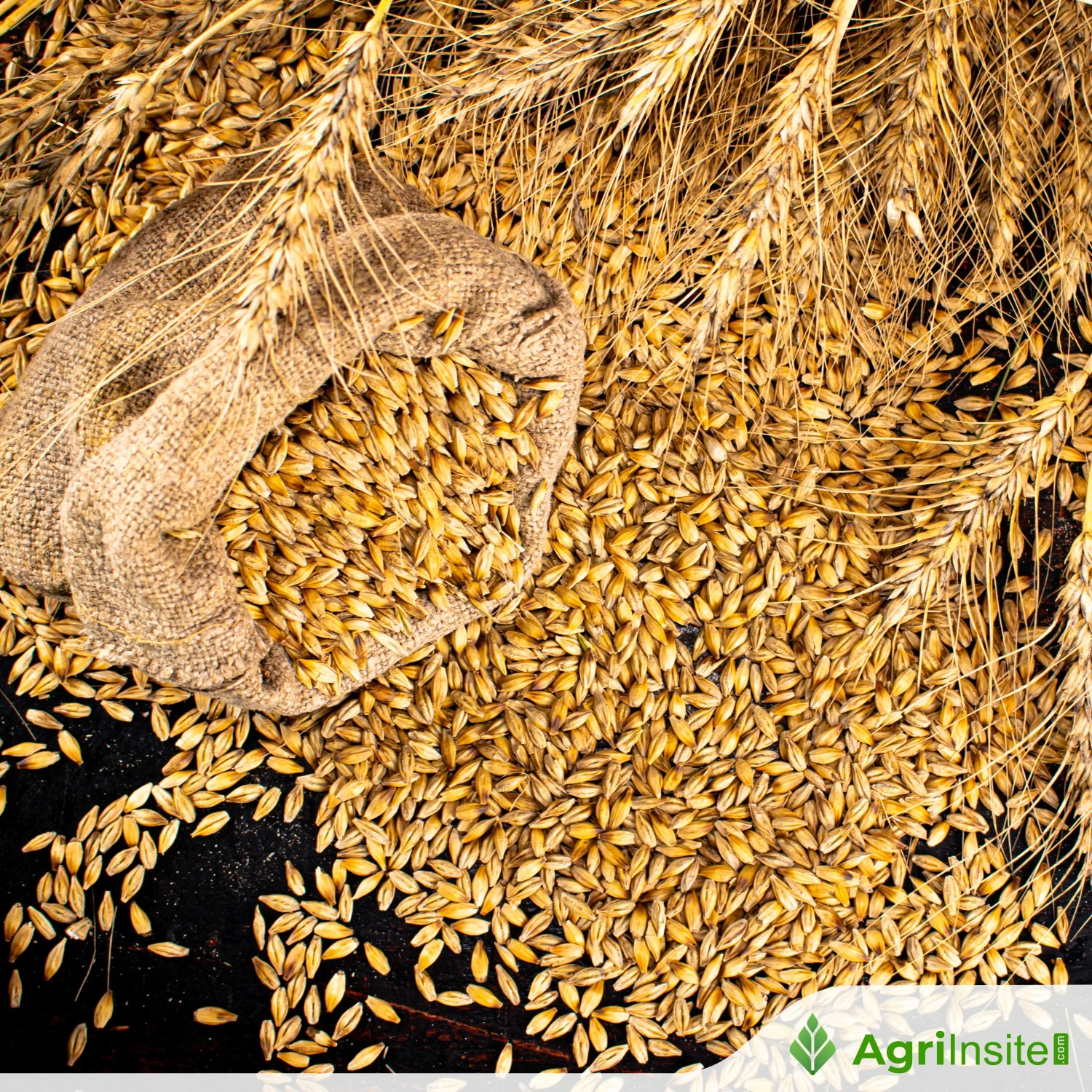
This article offers a fascinating glimpse into the production of Shredded Wheat at Cereal Partners’ Staverton factory. The detailed tour reveals the seamless, highly mechanized process, from wheat kernel hydration to the final crisp and packaged biscuits. While some trade secrets remain undisclosed, the description of vibrating conveyor belts, massive ovens, and precise packaging machinery paints a vivid picture of industrial efficiency. With potential investment on the horizon, the future of this iconic British breakfast staple appears promising.
The purest of foodstuffs, the crispest of breakfasts, the simplest of choices… what more can be said about one of Britain’s most recognisable breakfast items?
Shredded Wheat is produced by Cereal Partners, in a large factory in Staverton, and has been since it was moved from Welwyn Garden City in 2007. One morning at the end of February, the gates to this temple of fibre were opened to the Wiltshire Times.
A tour had been arranged, to be commandeered by cereal veteran and Staverton’s assistant performance manager Justin Hill, who began with an introductory lecture covering the basics, with a portentous and very true-sounding statement: “Not many companies can say their product is made of one ingredient.”
At the moment factory produces both Shreddies and Shredded Wheat, but guided by Justin, the Wiltshire Times followed the genesis, growth, and packaging of the iconic ‘Big Biscuit’ Shredded Wheat item.
The beginning of the process is much the same as the end, which is just like the middle – concerning wheat. Unimaginable quantities of recently-harvested wheat, produced, Justin says, by a family farm based near Northampton.
We began in a large room with a slightly grassy and wheaty aroma that was filled with industrial machinery, which perhaps to the surprise of only a few is what the rest of the factory is filled with.
After all, despite what the old Shreddies adverts used to suggest, to this reporter’s barely containable disappointment, Mr Hill clarified: “We do not actually employ knitting nanas, unfortunately.”
The tour proceeded by taking us to what is called the tower, where the creation of Shredded Wheat begins.
The wheat is first processed to extract the kernels, or ‘berries’, which are hydrated in large batch-cookers, which soak about a ton of ‘berries’ at a time. The ‘berries’ are then moved along a number of vibrating conveyor belts to shake off excess moisture before they are decanted into seven-ton silos.
From these, the berries are dropped through narrow cylinders onto a conveyor belt where the berries are dropped between rollers and crushed into strands that are then somehow layered – with the exact method employed remaining confidential.
What also could not be revealed was further information about the top-secret piece of equipment at the end of the line, which somehow chops the endless bunch of wheaty strands into recognisably biscuity shape, and spread said biscuits out across a wide and slow-moving conveyor belt.
At this stage, though Shredded Wheat-like in appearance, the ‘big biscuits’ are extremely moist – 47 per cent to be precise – and would hardly crunch at all if you were to close a fist around one of them.
To add said crunch, the big biscuits are delivered into a rather long oven, which stretches for as much as 50 yards, perhaps even 50 metres to be baked and toasted.
The final sections of the process involve packaging, a process that was certainly the most pleasantly surprising of all the stages: an endless sheet of the cereal’s recognisable snow-white paper packaging is launched at the biscuits as if from a spinning needle, covering two at a time that are then sealed off into a pouch.
This specific process is no less hypnotic than the rest of the production of Shredded Wheat – but the mechanised harmony of fine-tuned instruments is far from the only thing going on in the Staverton factory.
The 200+ employees that work on the site can bee seen dutifully and attentively at work on the factory floor. At the packing stage, Mr Hill introduced us to two relevant experts: Bartosz and Martin, who posed for photos beside the machine that sees the pouches enter the Shredded Wheat boxes.
Finally comes a large room full of large and highly precise machines awaiting the slow approach of the cereal boxes down conveyor belts, whisking them off to Melksham from where it is distributed to the nation.
Short and fleeting as the visit may have been, with proposals on the table that could see the factory receive £74 million in investment as the business mulls a closure in the Wirral, this interior, containing the serenest of machine processes, looks set for a long and illustrious future.
To read more about Wheat News continue reading Agriinsite.com
Source : Wiltshire Times
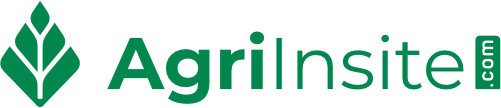