Universal Fuel Technologies’ Pilot Demonstrates New Sustainable Aviation Fuel Production Pathways

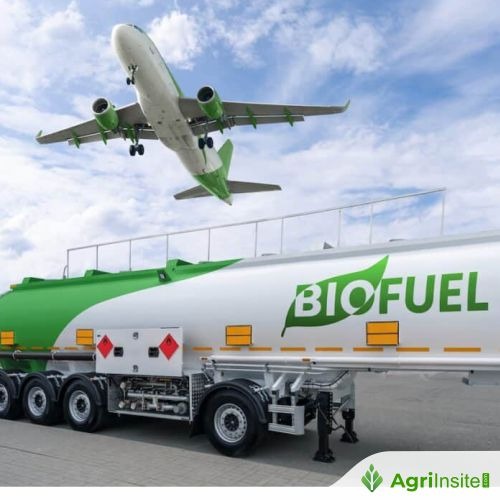
Universal Fuel Technologies (Unifuel) completed a five-month pilot project demonstrating its Flexiforming technology for Sustainable Aviation Fuel (SAF) production. Conducted at RPD Technologies in Texas, the project produced 100 liters of SAF, now undergoing ASTM certification. Flexiforming enables cost-efficient SAF production from ethanol, methanol, and renewable naphtha, offering a scalable solution for the aviation industry.
LOS ALTOS, Calif. : To support Sustainable Aviation Fuel (SAF) production goals and increase feedstock availability, Universal Fuel Technologies (Unifuel) has completed a successful five-month pilot project. The campaign demonstrated the effectiveness and viability of the company’s Flexiforming technology in producing SAF that is chemically comparable to conventional jet fuel from various renewable feedstocks. The project was conducted at the facilities of RPD Technologies in Crosby, Texas, from August through December of last year. It produced nearly 100 liters of SAF sample material under stable process conditions, signaling readiness for the technology to scale up. The campaign focused on converting methanol and ethanol to SAF and ethanol with paraffinic renewable naphtha made via Hydroprocessed Esters and Fatty Acids (HEFA) to SAF. Samples of Unifuel’s Flexiforming SAF have been thoroughly tested and are now being analyzed at Washington State University’s Bioproducts, Sciences, and Engineering Lab for Tier 0 screening—the initial step of the SAF certification process.
“As an industry, it’s crucial that we continue to support and explore new technologies to advance SAF to match the functionality of petroleum-derived jet fuel,” said Joshua Heyne, Director of the Bioproducts, Sciences and Engineering Lab (BSEL) at Washington State University. “The capability to make aromatic molecules and process various feedstocks through a single technology platform not only streamlines SAF production but also significantly lowers production costs, making it more economically viable and accessible for producers and airlines.”
The pilot yielded two distinct forms of SAF: Synthetic Aromatic Kerosene (SAK), an essential aromatic blend component for maintaining compatibility of paraffinic SAF with the composition of fossil kerosene, and a 100% drop-in, fully synthetic SAF that contains the correct aromatic content for commercial use, pending certification by ASTM International, the leading global technical standards organization. As a result, the aromatic component of SAF produced through Flexiforming, made from HEFA and FT naphtha, can be blended with the primary paraffinic SAF stream from these units. This creates the opportunity to produce drop-in SAF directly at HEFA and FT units, reducing the costs and complexity of the logistics and aiding in industry adoption.
“The impact of this pilot project reaches far beyond technical validation,” said Alexei Beltyukov, CEO of Universal Fuel Technologies. “A considerable value of Flexiforming is that it contributes to making SAF fully interchangeable with fossil jet fuel once ASTM approved. Because of its aromatic properties, which are essential for compatibility with today’s aircraft, Unifuel’s SAK can be blended with paraffinic SAF from HEFA or FT and sold directly to airlines without the need for blending with another fuel. As the aviation industry faces increasing pressure to reduce its environmental impact and contain costs, technologies like Flexiforming could be crucial in scaling up sustainable aviation fuel production to keep pace with demand.”
Flexiforming provides several options for SAF production, making it especially adaptable for various renewable fuel scenarios. The pilot campaign validated ethanol-to-jet (ETJ), methanol-to-jet (MTJ), and renewable naphtha-with-ethanol-to-jet (NETJ) production routes, offering flexibility in feedstock selection. Due to the technology’s substantially lower energy and hydrogen requirements, Unifuel estimates Flexiforming to be half the cost of current ETJ processes. Moreover, Flexiforming allows renewable fuel plant operators to upgrade low-value byproduct naphtha from existing HEFA or Fischer-Tropsch (FT) processes to create high-value aromatic SAF that can be blended into fully synthetic drop-in-ready jet fuel.
“The samples of Unifuel’s Flexiforming SAF candidates show promise to proceed to full certification as aviation turbine fuel,” said Harrison Yang, Research Assistant Professor of the BSEL at Washington State University.
Unifuel’s team has completed over a decade of research and extensive testing on its Flexiforming technology. As Unifuel transitions to the next stage, samples of the Flexiforming SAF produced during the campaign are being prepared for ASTM certification submission. This certification process is essential for validating the fuel’s safety and performance characteristics, ultimately determining its viability for commercial aviation use. To learn more about Unifuel’s journey toward revolutionizing sustainable fuel production, visit unifuel.tech.
About Universal Fuel Technologies
Universal Fuel Technologies is a technology licensing company committed to advancing sustainable fuel production through its Flexiforming chemical process. Cost and energy-efficient, Flexiforming converts renewable feedstocks to drop-in-ready sustainable aviation fuel (SAF). Offering unparalleled flexibility in feedstock selection and scale of deployment, the company helps plant operators easily adapt to market conditions. Flexiforming is compatible with any alcohol feedstock and complements existing SAF processes by upgrading naphtha and LPG to high-value SAF. Backed by a decade of research and over 6,000 hours of testing, Universal Fuel Technologies supports the industry’s transition to renewable fuels with technology that results in fewer carbon emissions and higher revenue generation. To learn more about Universal Fuel Technologies, please visit unifuel.tech.
To read more about Ethanol Industry & Bio Energy News, continue reading Agriinsite.com
Source : Business Wire
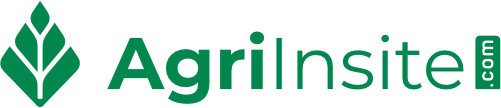