Why Maharashtra sugar mills are turning to machines for harvesting cane

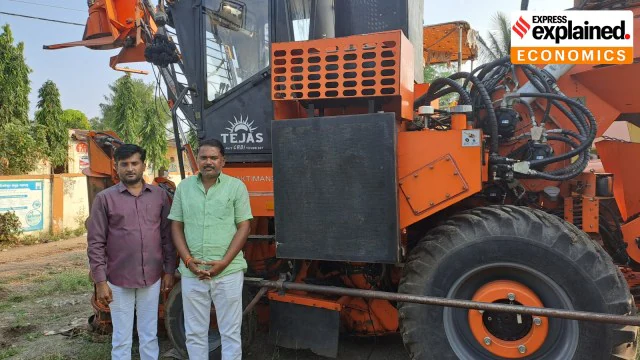
Labour shortages in Maharashtra’s sugarcane harvesting, driven by alternative employment opportunities and welfare schemes, are pushing mechanisation. Sugar mills like Manjara Cooperative in Latur have adopted mechanical harvesters, achieving over 90% mechanisation. Machines improve efficiency but raise costs and eliminate cane tops used as cattle fodder. Entrepreneurs investing in these harvesters report profitability despite high upfront costs. Experts predict a gradual shift to mechanisation, with some mills targeting 50% machine-harvested cane in five years. Challenges remain in balancing labour needs and modernisation.
Getting labour for agricultural operations has become a recurrent problem.
The reasons: The drudgery of transplanting paddy, spraying pesticides or picking cotton; the opening of alternative employment avenues (in construction, manufacturing and informal services); and government welfare schemes (MGNREGA, free food and direct cash transfers). These have raised the “opportunity cost” of such backbreaking work, to make these no longer the default occupation of rural labourers.
Labour shortages, in turn, have spurred farm mechanisation and even sales of herbicides to replace manual weeding
A significant story of mechanisation, unfolding in Maharashtra, is in sugarcane harvesting.
The current system
In Maharashtra, unlike in Uttar Pradesh and most other cane-growing states, it is the sugar mills and not farmers who undertake harvesting.
The factories enter into contracts with muqaddams (middlemen) to organise tolis (labour gangs) for harvesting cane in farmers’ fields. The muqaddam in charge of a toli — each comprising 10 man-woman pairs of labourers — is typically paid an advance around June to bring them during the cane crushing season from November till April.
A single labourer-couple can harvest 2-2.5 tonnes of cane per day, amounting to 20-25 tonnes for a toli. A factory crushing 5 lakh tonnes (lt) of cane over a 150-day season would, thus, require roughly 150 tolis or 3,000 labourers.
Maharashtra has an estimated 12-12.5 lakh cane-harvesting labourers. Around 8-8.5 lakh work in the state — the mills are largely in western Maharashtra and the adjoining Marathwada districts of Dharashiv and Latur — while the rest go to Karnataka and Gujarat. The bulk of them are migrants coming from Beed, Ahmednagar, Hingoli, Nanded and Yavatmal (mostly belonging to the Banjara/Lambani and Vanjari Other Backward Class communities), and also Amravati and Nandurbar (mainly adivasi tribals).
The muqaddam is responsible for recruiting the labourers, besides supervising them and coordinating with the mill staff. The cane in each field — 5 lt would cover over 7,000 hectares, at an average 70 tonnes/hectare yield — is harvested as per a pre-planned schedule, to guarantee uninterrupted supply during the crushing season.
The harvesting labourers are paid Rs 366/tonne now. This is a rate fixed by the Maharashtra government as a tripartite agreement with the labourers’ state-level unions and the millers’ association. The muqaddam receives a commission on top, normally 20%, from the factories. Being paid at the end of the season, it incentivises him to ensure that the labour not only comes, but works and does not leave midway. A muqaddam (contractor) taking labourers from Maharashtra’s Beed district to a mill in northern Karnataka. (Photo: Harish Damodaran)
The whole system, however, hangs by a slender thread. There are instances where mills pay the advance to the muqaddam, who distributes it to the labourers and they ultimately don’t turn up. Sometimes, labour isn’t available and crushing cannot start because of elections — as has happened this season. Moreover, the harvesting labour force is itself aging, with the next generation having basic education and not keen to do the work of their parents.
Mechanical harvesters
In 2020-21, the Manjara Farmers’ Cooperative Sugar Factory at Latur deployed 10 cane harvesting machines on an experimental basis. That number rose to 13 in 2021-22 and to 44 in the 2022-23 crushing season, which saw 75% of the mill’s cane being mechanically harvested.
During 2023-24, about 93% of the total 6.61 lt cane crushed from 9,000-odd hectares was harvested by 49 machines. “This season, we will be India’s first sugar mill to achieve 100% mechanical harvesting,” said P S Desai, managing director of the Manjara factory, which now has 55 harvesters manufactured by CNH Industrial (New Holland brand) and Tirth Agro Technology (Shaktiman).
Out of the 55, only seven are mill-owned. The rest are with private entrepreneurs, who have been provided loans by the Latur District Central Cooperative Bank (LDCCB) against the guarantee of the factory lifting the machine-harvested cane (the Manjara cooperative was founded by the former Maharashtra Chief Minister, Vilasrao Deshmukh; his Dhiraj, is the LDCCB’s chairman).
The mechanical harvester owners are being given Rs 475/tonne, more than the Rs 439 for manual harvesters after adding the 20% muqaddam commission. “But we don’t have to worry about labourers not coming or running away. Earlier, we had 80-100 factory staff just to deal with the muqaddams and tolis. Today, 24-25 are needed to oversee 55 machines,” Desai said.
The machines cut the whole cane from the bottom. The knives of the manual harvesters usually don’t go that low and leave behind 4-6 inches of cane on the ground. Since the lower part of the cane has more sugar, it also translates to lower recovery during crushing.
Moreover, March onwards, the efficiency of harvesting and cane arrivals, too, is reduced as the temperature starts to rise, adding to further stress on the labourers. They, then, charge extra from the farmers to harvest their cane.
The Manjara cooperative paid its farmer-members a cane price of Rs 2,700 per tonne in 2023-24, which excluded harvesting and transport charges of Rs 809.96. The Manjara Group – now under the late Vilasrao Deshmukh’s brother, Diliprao — has 10 mills in all (five of them private) that together crushed 53.02 lt of cane in the last season.
“He (Diliprao) has set a target of 50% mechanical harvesting for the other nine mills in the new 2024-25 season,” Desai said.
Pros and cons
Sachin Shinde has invested Rs 90 lakh in a 173-horsepower ‘Shaktiman’ sugarcane harvester, plus Rs 10 lakh each in two infielders. These, attached to 55-hp tractors (two of them, costing another Rs 10 lakh each), move parallel to the harvester and collect the cut cane in a hydraulically-operated cage.
The 39-year-old — who also grows sugarcane on 15 out of his 45-acres land in Sawargaon village of Latur district — has overall spent Rs 1.3 crore, 90% of it financed by a LDCCB loan at 10% annual interest. In 2022-23, he harvested 12,500 tonnes. Last season, he harvested 19,500 tonnes, and grossed Rs 92.62 lakh at Rs 475/tonne.
Shinde has hired two harvester operators (at Rs 50,000/month each) and four infielder drivers (Rs 20,000/month each). His outgo on labour, replacement of cutting blades and machine maintenance is Rs 15 lakh. The cost of diesel (average 2.25 litres per tonne of cane), at Rs 92/litre, is Rs 40.4 lakh on 19,500 tonnes. That still leaves a decent gross margin.
A major drawback of the mechanical harvesters is that they cut not just the whole cane, but also the green top leaves fed to animals. In states such as UP, the fodder needs of buffaloes and cattle during the winter and spring months are basically met by cane tops. The harvesters release the tops into the field through an extractor fan after chopping them into very small pieces, which cannot be easily collected for fodder purposes.
But Shinde claimed that the cane tops left in the field help enhance soil organic matter. They also act as mulch (cover) for the soil, protecting it against water loss and excess heat or cold.
B B Thombare, chairman of Natural Sugar & Allied Industries Ltd, felt that mechanical cane harvesting is inevitable, “but will be a gradual process”. His factory at Ranjani in Dharashiv district’s Kalamb taluka, which crushed 9.45 lt of cane last season, has 25 harvesting machines. These harvested 20% of its cane, “which may go up to 50% in five years’ time”.
To read more about Sugar Industry continue reading Agriinsite.com
Source Link : Indian Express
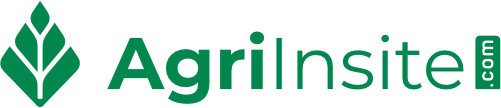